Bob Stasonis
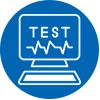
Guide for Automated Test Best Practices | Part 3 Optimize Test System
September 27, 2023
Part 3 | Test System Integration, Deployment and Sustainability This is part 3 of our three-part series on automated test best practices. For best..
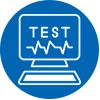
Guide for Automated Test Best Practices | Part 2 Deploying Test Systems
August 17, 2023
Part 2 | The Enjoyment of Deployment - Automated Test Best Practices As mentioned in Part 1 of this blog series, printed circuit boards (PCBs) are..
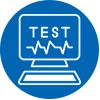
Guide for Automated Test Best Practices | Part 1 Test System Design
July 27, 2023
Part 1 | The Three Most Important Things in Test System Design: Communicate, Communicate, Communicate Intro I don’t think anyone reading this blog..
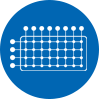
What is the Right Platform for My Automated Test System Switching?
December 19, 2022
When it comes to switching for an automated test system, there are many choices. Vendor, specifications, cable types, switching routing software,..
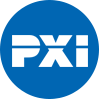
Electronic Testing 101: The High Points of High Voltage Testing - Part 1
August 3, 2022
When ICs replaced vacuum tubes and CRTs were replaced with flat LCD screens, test engineers probably thought that working with high voltage was a..
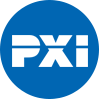
Electronic Testing 101: The High Points of High Voltage Testing - Part 2
August 3, 2022
In our last post about high voltage testing, we talked about relay types, density, and specifications. Now let's look at the possible test system..
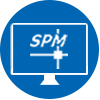
Electronic Testing 101: The Hard Part of Software in Complex Switching Systems
March 24, 2022
Now that you know all about matrices, let’s start programming them. Open this relay, close that one, repeat. Easy, right? Let’s look at the..
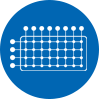
Electronic Testing 101: The Correct Way to Use a Crosspoint Matrix
March 16, 2022
In our last blog post, "Electronic Testing 101: Switch Types & Configuration – Part 3," I provided details on what a matrix is and several different..
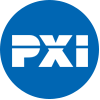
Operating Software and Programming Languages for the PXI/PXIe Platform
March 9, 2022
When it comes to the PXI and PXIe platforms, there are a few software options available depending on your requirements. The PXI standard defines the..
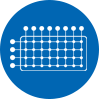
Electronic Testing 101: Switch Types and Configurations – Part 3
February 7, 2022
OOPS, I left out one configuration in my last post:Transfer Switch – Essentially, a Transfer switch is a double-pole/double-throw (DPDT) design for..