Posts about
PXI/PXIe
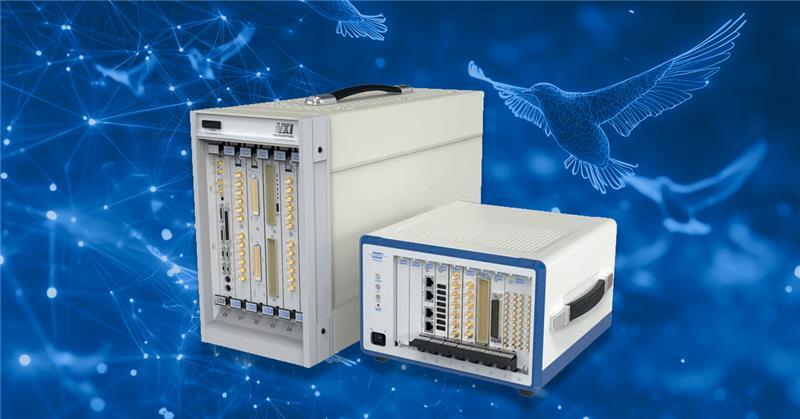
Migration from VXI to PXI Testing Systems – A Practical Comparison
June 26, 2025
In today's rapidly evolving technological landscape, transitioning from VXI (VME eXtensions for Instrumentation) to PXI (PCI eXtensions for..
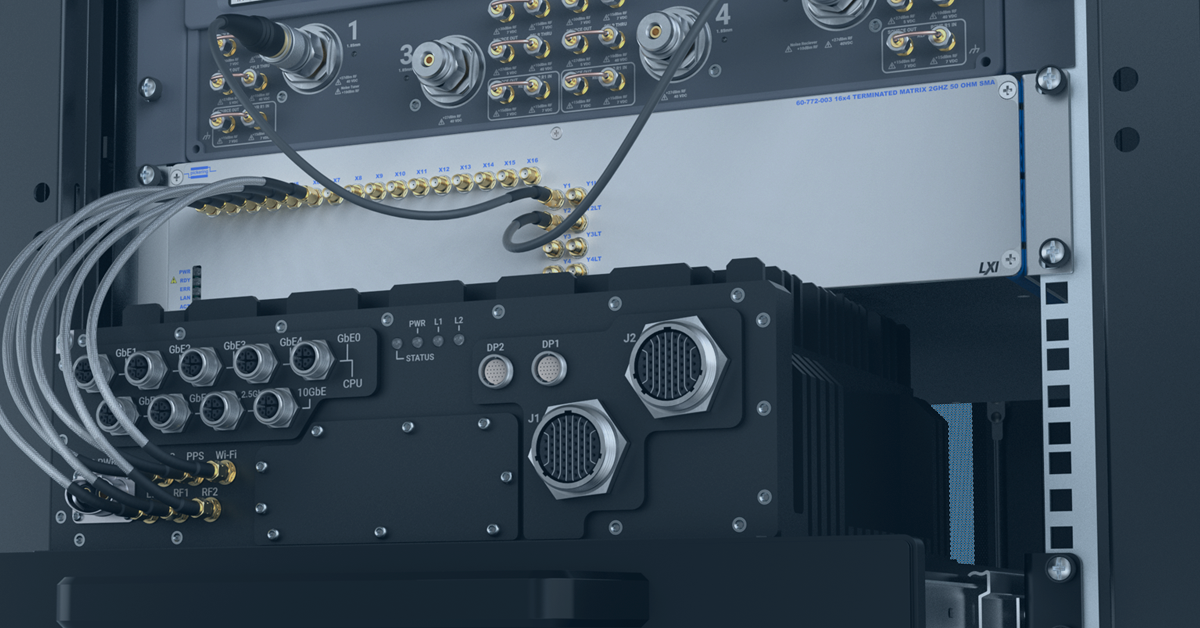
Best Practices to Accelerate RF & uWave Testing
November 18, 2024
As an established engineering company specializing in switching and simulation solutions for test and measurement, we’ve encountered numerous..
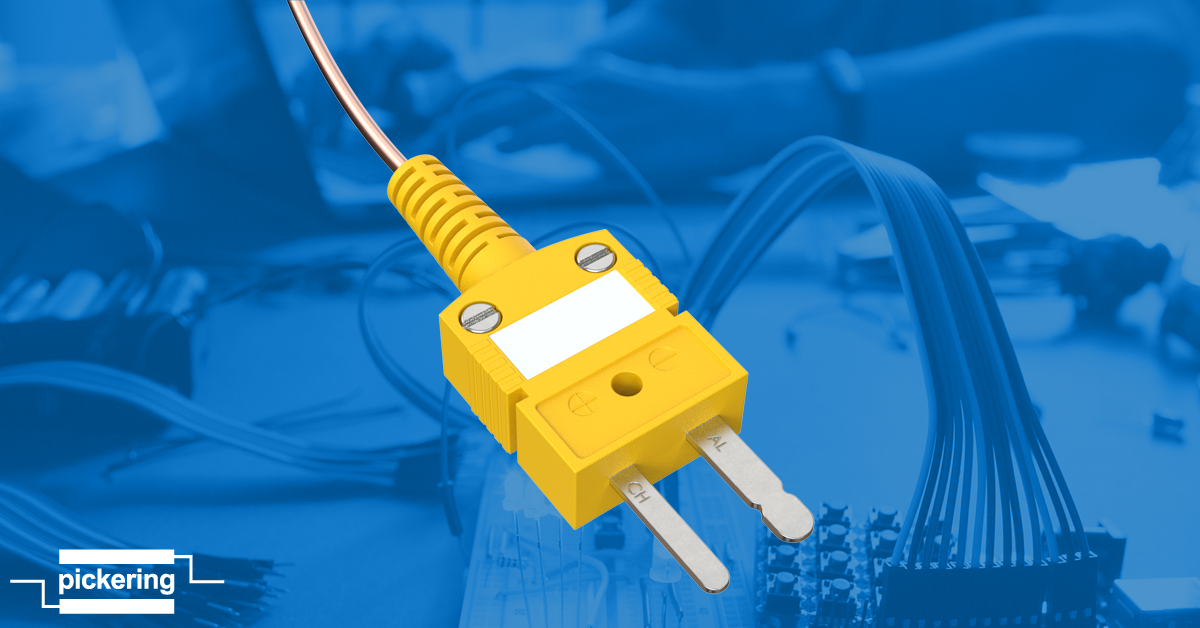
Thermocouple Simulation in ECU Validation (Part 2 of 6)
June 25, 2024
Note: This article is the next part of our six-part series on sensor simulation in ECU validation. Part 1: Understanding Sensor Simulation in ECU..
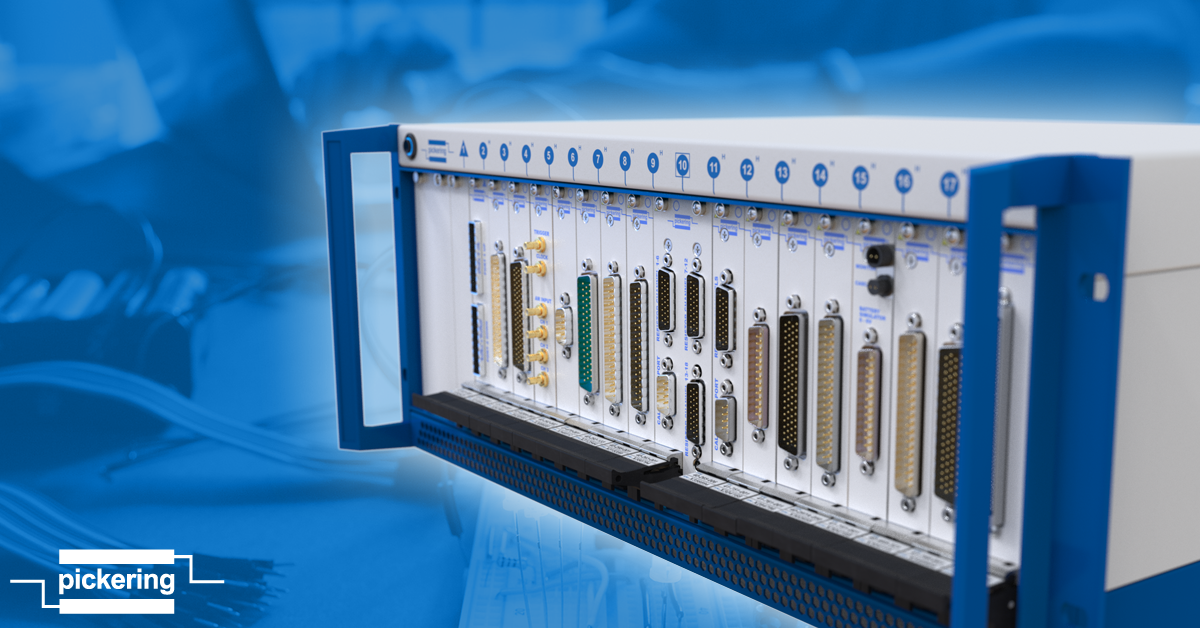
Understanding Sensor Simulation in ECU Validation (Part 1 of 6)
June 12, 2024
Sensors play a pivotal role in ensuring the reliable operation of most transportation options we depend on today. An aircraft is an excellent example..
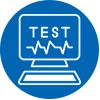
Comprehensive Guide to PXI RF Switching: MEMS vs. EMR and Solid State
November 30, 2023
In the world of test and measurement, precision, efficiency, and adaptability are essential to success. MEMS, which stands for Microelectromechanical..
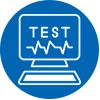
The Value of HIL Simulation in Rocket Development: The Key to Reliable Testing
November 16, 2023
In the space industry, the consequences of failure are incredibly high. Testing is not just a routine checklist; it's a matter of mission success and..
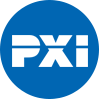
Bridging the Gap Between PXI & PXIe: You Don’t Have to Choose
October 23, 2023
In the ever-evolving world of technology, where suppliers must actively manage a wide and varied installed base while continuously innovating new..
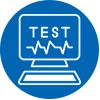
Guide for Automated Test Best Practices | Part 3 Optimize Test System
September 27, 2023
Part 3 | Test System Integration, Deployment and Sustainability This is part 3 of our three-part series on automated test best practices. For best..
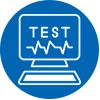
Guide for Automated Test Best Practices | Part 2 Deploying Test Systems
August 17, 2023
Part 2 | The Enjoyment of Deployment - Automated Test Best Practices As mentioned in Part 1 of this blog series, printed circuit boards (PCBs) are..
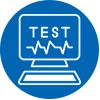
Guide for Automated Test Best Practices | Part 1 Test System Design
July 27, 2023
Part 1 | The Three Most Important Things in Test System Design: Communicate, Communicate, Communicate Intro I don’t think anyone reading this blog..