Posts about
Automated Test System
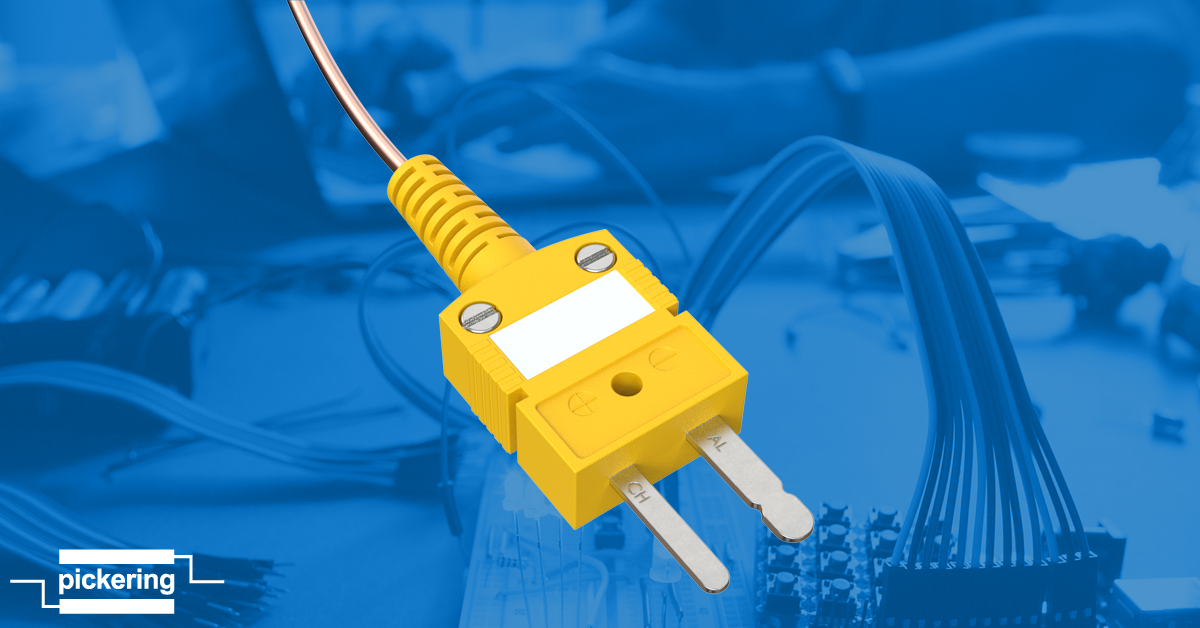
Thermocouple Simulation in ECU Validation (Part 2 of 6)
June 25, 2024
Note: This article is the next part of our six-part series on sensor simulation in ECU validation. Part 1: Understanding Sensor Simulation in ECU..
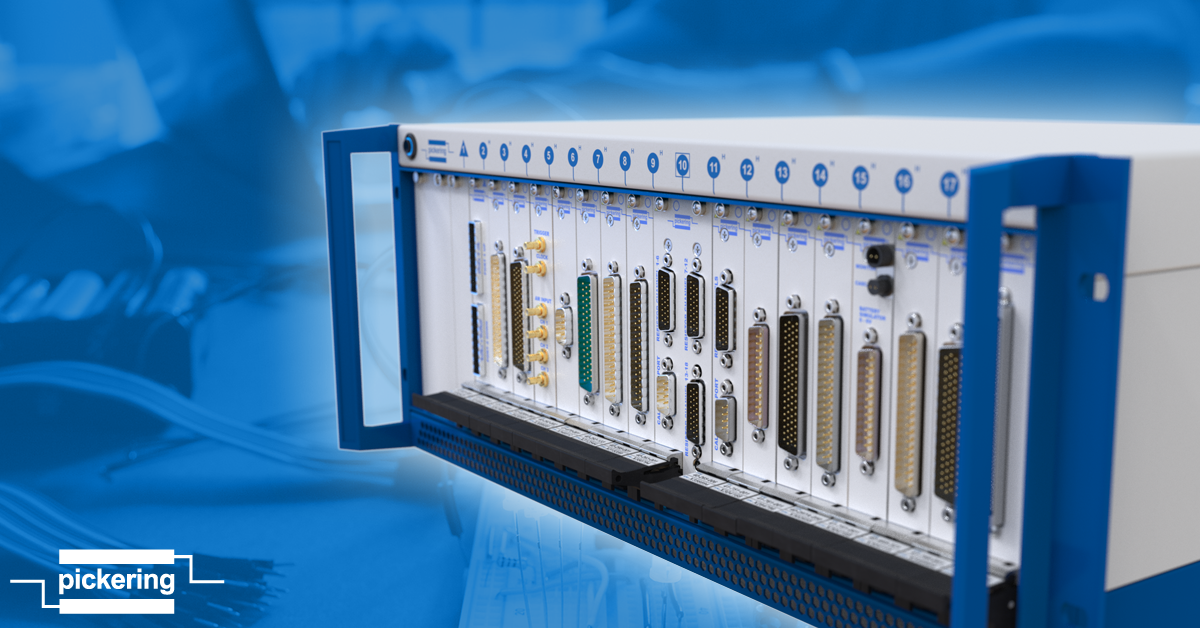
Understanding Sensor Simulation in ECU Validation (Part 1 of 6)
June 12, 2024
Sensors play a pivotal role in ensuring the reliable operation of most transportation options we depend on today. An aircraft is an excellent example..
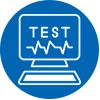
The Value of HIL Simulation in Rocket Development: The Key to Reliable Testing
November 16, 2023
In the space industry, the consequences of failure are incredibly high. Testing is not just a routine checklist; it's a matter of mission success and..
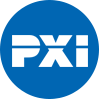
Bridging the Gap Between PXI & PXIe: You Don’t Have to Choose
October 23, 2023
In the ever-evolving world of technology, where suppliers must actively manage a wide and varied installed base while continuously innovating new..
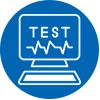
Guide for Automated Test Best Practices | Part 3 Optimize Test System
September 27, 2023
Part 3 | Test System Integration, Deployment and Sustainability This is part 3 of our three-part series on automated test best practices. For best..
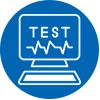
Guide for Automated Test Best Practices | Part 2 Deploying Test Systems
August 17, 2023
Part 2 | The Enjoyment of Deployment - Automated Test Best Practices As mentioned in Part 1 of this blog series, printed circuit boards (PCBs) are..
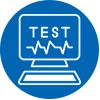
Guide for Automated Test Best Practices | Part 1 Test System Design
July 27, 2023
Part 1 | The Three Most Important Things in Test System Design: Communicate, Communicate, Communicate Intro I don’t think anyone reading this blog..
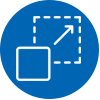
Advanced Test Systems: Modular PXI, PXIe and LXI/USB Chassis Solutions
July 13, 2023
Introduction: In today's dynamic technological landscape, achieving optimal testing and simulation processes requires a strategic approach that..
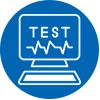
Creating a Test System for Longevity
March 28, 2023
As a test program manager, it's important to understand how to design and build a test system that will last an entire product lifecycle. But what..
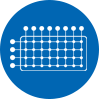
What is the Right Platform for My Automated Test System Switching?
December 19, 2022
When it comes to switching for an automated test system, there are many choices. Vendor, specifications, cable types, switching routing software,..